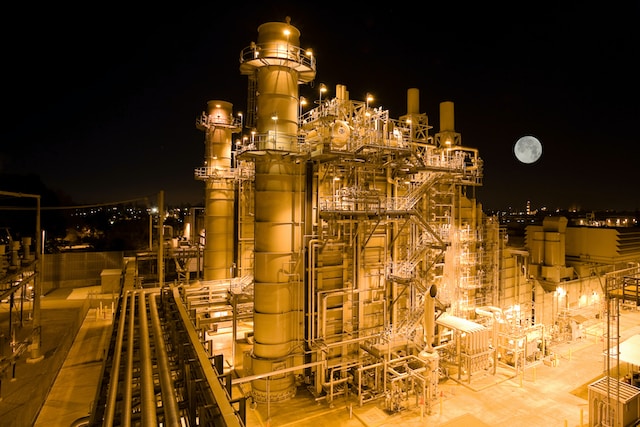
How Hydraulic Filter Suppliers Works
Hydraulic filter suppliers remove contaminants from hydraulic fluid as it cycles back to the reservoir. This keeps the hydraulic system clean and prevents contamination ingression that accelerates equipment wear.
Dirt, sludge, metal particles, water, and chemical byproducts in hydraulic systems can clog critical or close-tolerance areas and lead to costly mechanical failure. The hydraulic filter is vital in preventing these damaging particles.
Hydraulic filters are essential components in hydraulic systems, ensuring the removal of contaminants to maintain optimal performance. Choosing reliable hydraulic filter suppliers VA is crucial for the longevity and efficiency of hydraulic equipment.
Paper Media Filters
Filter media for hydraulic filters must be engineered to meet the specific fluid power application. This includes product viscosity, temperature, chemical compatibility, and flow rates. In addition, the micron rating of the filter must be considered.
Micron ratings are either nominal or absolute. A nominal micron rating measures the percentage of particles the filter removes that are the same or more significant than a stated size. An absolute micron rating takes out all the particles that are the same or more significant than the rated size.
The choice of filter media for hydraulic filters has to be carefully balanced with cost. High-efficiency media with petite pore sizes increases the mean time between hydraulic component failures. However, this must be weighed against the cost of purchasing and replacing elements and maintaining filtration equipment. A proper fluid conditioning can improve ultra-fine filtration’s cost/benefit ratio.
Metal Fiber Filters
Hydraulic pumps, motors, and cylinders require clean hydraulic fluid to function correctly. Solid contamination is the leading cause of such systems’ malfunction, failure, and early degradation.
To improve the efficiency of hydraulic systems, filter manufacturers are focusing on metal filter design innovations to ensure that contaminant particles are removed from the system as quickly as possible. These improvements will reduce hydraulic equipment’s maintenance and repair costs, increase operating safety, and extend component life.
One way to achieve this goal is to use a metal fiber filter. This type of filter is made from a three-dimensional filtration medium containing hundreds of metallic fibers fused into a woven felt material. To construct the material, manufacturers utilize alloys similar to those used for woven wire mesh, such as stainless steel or aluminum. The resulting element has a high dirt-holding capacity and provides excellent differential pressure stability. It is also highly corrosion-resistant.
High-Pressure Filters
High-pressure filters protect hydraulic components downstream from catastrophic pump failure. These cartridge-style filters filter fluid through a woven media and offer high flow rates with minimal differential pressures to avoid early component wear. They are the best investment for critical circuits such as servo lines.
Hydraulic system components often operate with only boundary lubrication, especially during cycling or changing loads. These conditions cause metal parts to wear against each other, creating microscopic particles. These particles are drawn into the hydraulic fluid and carried to other parts, where they can create additional wear. This process, called abrasive wear, can destroy expensive hydraulic equipment.
If unchecked, microbes – minute life forms that can cause system failure – grow exponentially in a dirty hydraulic fluid environment. These microbes produce acids and other waste products that attack most metals. A filtration system can prevent this by trapping and holding the microbes. Choosing a filter with the highest possible dirt-holding capacity for your hydraulic fluid is recommended for the best results.
Low-Pressure Filters
It is crucial to keep fluid clean to protect expensive hydraulic system components. This is accomplished by deploying filters that trap the contaminants in the oil before they reach sensitive components such as hydraulic pumps, actuators, and valves. Ideally, hydraulic system components are filtered at every stage of the circuit – in the reservoir, before and after pumps, in return lines, and off-lines. However, cost often limits the amount of filtration a system can implement.
When choosing a filter element, consider the micron rating and pressure capacity. The smaller the filter’s pore size, the more fine-tuned its ability to trap particles. The higher the pressure rating, the more stress the filter can handle without compromising its ability to trap fine particles. Check the equipment manufacturer’s manual for recommended pressure and micron ratings. This will ensure the hydraulic filter can meet the demands of your equipment. An adequately rated filter will protect your machinery for longer and reduce the risk of unexpected failures resulting in costly downtime.

